MIG Welding Basics – Pros & Cons
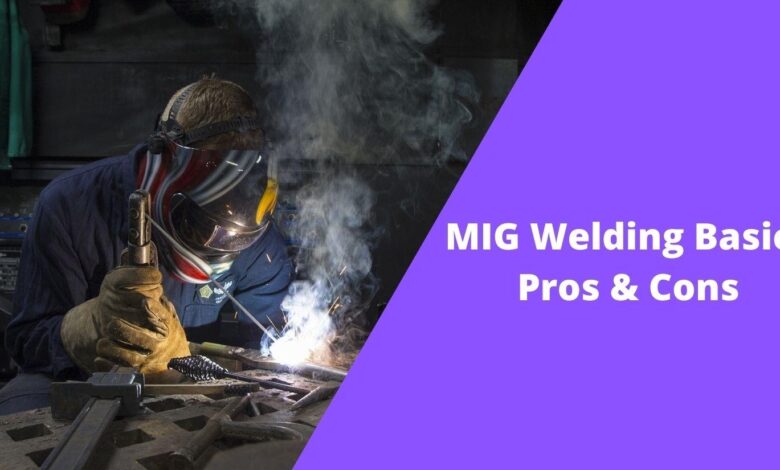
Welding is an essential skill for moderate and even hardcore enthusiasts. Bolts and nuts will only take you so far. If you are serious to break through the custom fabrication industry, you are going to have to learn the basics of MIG welding right away.
The useful skill of MIG welding opens up new custom fabrication options for your projects that you once considered impossible.
Although attending a seminar or a welding class is a good idea, proper equipment, practice, and patience are the three elements you need to master this skill. There’s a lot to learn before you enter the world of MIG welding. We will start with the general idea of MIG welding to get everyone up to speed.
Gas metal arc welding is the proper name for MIG welding. It is the most common welding technique in the fabrication industry and for good reasons- it is inexpensive, fast, and produces quality welds. Moreover, novice welders get a hold of MIG welding easily.
According to Welding Rage, MIG welders are the best machines for novice welders to start their career in welding. With a little practice and dedication, you can expect to start making good welds in a week.
Even a novice welder or a beginner can handle basic fabrication and repair tasks if he has the right knowledge, equipment, and setup. Your MIG welding unit will become more than a learning machine- it will be your go-to tool for repairing your car’s panels, welding pans of the new floor, and fixing your garden equipment.
Working principle

MIG welding was first introduced in the early 1940s. The general working principle is pretty much the same, even after 60 years. The MIG welder creates a short circuit between a cathode and a continuously fed anode using an arc of electricity. The non-reactive inert gas and the heat produced from the short circuit melt the metal and induce a joint.
Once the metal stop receiving heat, it cools down and solidifies – giving you a fused metal and hence, a strong weld.
Just a few years ago, the welding technique MIG or metal inert gas was changed to GMAW or gas metal arc welding. However, the name ‘MIG’ has will stick for the better days.
A welding operator needs to learn and establish the basic technique to maximize performance, productivity and achieve quality welds. We have to follow the standard welding procedure; from using proper travel speeds and MIG gun angle to employing safe ergonomics.
The proper way to perform MIG welding is to:
- Place the fume extractor just above the welding area
- Use the ground clamp to make adequate ground and secure the welding object
- Loosen the adjusting screw on the gas cylinder
- Use the handwheel to open the gas cylinder
- Adjust the turning screw clockwise until the gauge reaches 15 CFH
- Turn on the MIG welder
- Adjust the wire feed speed and secondary voltage
- Ensure that an appropriate amount of wire is present with the welding torch
- Use the MIG welding techniques to join the components
- Turn the voltage and wire feed settings to the lowest after you are finished
Pros
MIG welding was developed for non-ferrous materials and aluminum. But it grew to be the most common welding technique with the advent of time. If we are to quote on its popularity, we would start with the advantages:
MIG welding process is convenient and easy to learn
You only need to pull the welder’s trigger to start MIG welding. Thus, it is a one-hand operation that any amateur welder can learn in a short period. The shielding gas, current, and wire feeding start to flow after pressing the trigger.
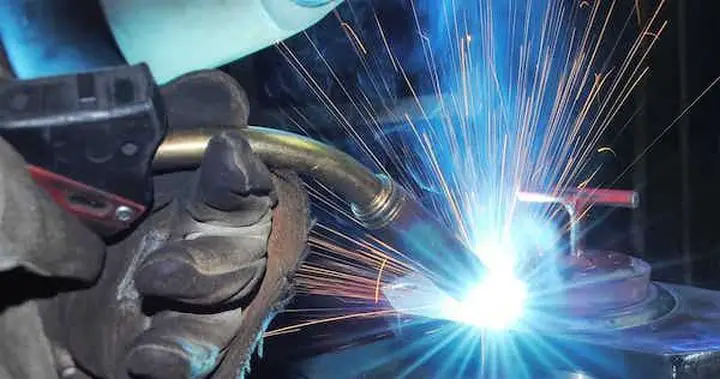
The advanced features in the welders such as the auto-feed wire system allow you to maintain control over the process.
Long-pass welding
You deposit more metal with each pass of the welding torch. Although you can’t justify this advantage on a small weld you can do the job greatly if you ever involve in complex and long welds. It means that you can complete your project with fewer passes. It does not only increase your efficiency but productivity as well.
Deep weld penetration
MIG welding offers deep weld penetration for a smooth and strong bead. Moreover, you can achieve quality welds on various metals of different thicknesses. Just get your head around the accurate amperage settings and you are good to go.
Cons
MIG welding has its disadvantages too, such as:
The setup cost is high
A good MIG welding machine is a big investment. The tools are usually designed for maintenance and repair at the component level. Therefore, repairs and maintenance costs are another headache.
Less portability
MIG welding loses a lot of points due to heavy welding units. A typical MIG welder machine is weighed around 25 to 85 pounds.
Weird welding positions
You might need to look for a new welding technique if your project includes overhead or vertical welding, high mobility, and heat input of the weld puddle.
Which metals can you weld with MIG welding?
Metals with higher weldability retain great weld quality. You have to study a few factors before choosing the welding material for MIG welding. For instance, the ideal metals for MIG welding are aluminum, stainless steel, and carbon steel.
The main parameters to determine the weldability of a material include the type of shielding gas, the cooling rate, the welding speed, and the electrode materials. Every metal can be welded to a certain extent. However, there are clear disadvantages and benefits to each.
Other than carbon steel, aluminum, and stainless steel, you can also weld silicon bronze, nickel, copper, magnesium, and other alloys.
How to start welding as a career?
A welding career is more rewarding and thriving than ever. For instance, underwater welders are earning more than $300,000 annually while certified welding inspectors are earning more than $72,000 per year.
You too can become a professional welder through recognized certification programs and rigorous training. It is all about developing your welding skill and having a keep interest in the industry.
Here are some steps to becoming a professional yet highly-paid welder:
Research all about welding
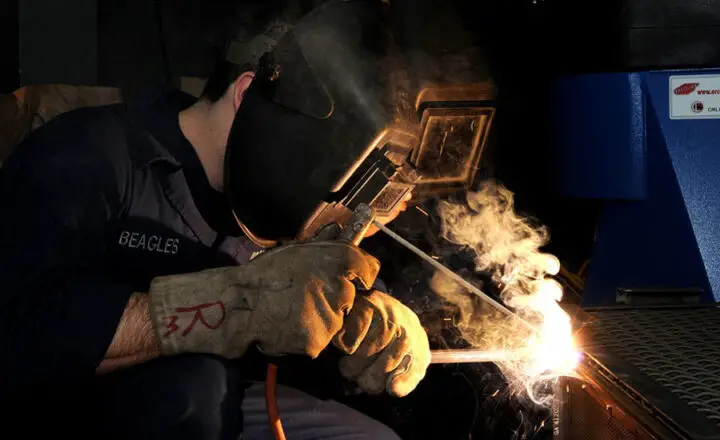
Know all about the demanding yet thriving profession. You have to get in touch with a couple of welders and get to know everything about the typical day of a professional welder. Make sure you are genuinely interested in this field.
Research about the safety hazards and do not forget to undergo all the medical tests. If you are really getting into the welding industry, a physician must evaluate your medical condition.
Get the education, vocational training, and the experience
There’s a mere difference between a professional welder and a good welder. Even though it is a skill-based profession, you need to enroll at a certification center or a community college to secure a good job.
Find the right discipline
If you are starting to look at welding as a career, make sure to explore all the disciplines- TIG, MIG, arc, and stick welding.
Obtain the necessary certifications
You have to obtain the certification and pass a skills test from the American Welding Society to become a licensed welder.
Grow your skills and gain experience
Once you find the right discipline, complete the certifications or vocational training, and secure a professional job, do not stop. Keep polishing your skills and explore other disciplines of welding as well. Opportunity knocks surely when you have multiple doors to open.
Verdict
Welding is an incredible yet lucrative career opportunity for anyone with any educational background. You can explore various local educational options in your locality and start your journey to become a successful welder.
Even though vocational training takes years, you can earn certifications in a matter of months and start earning. However, you have to be passionate about welding. It is a skill-based profession but it requires a constant passion to move forward.