What is Investment Casting and How Does It Work
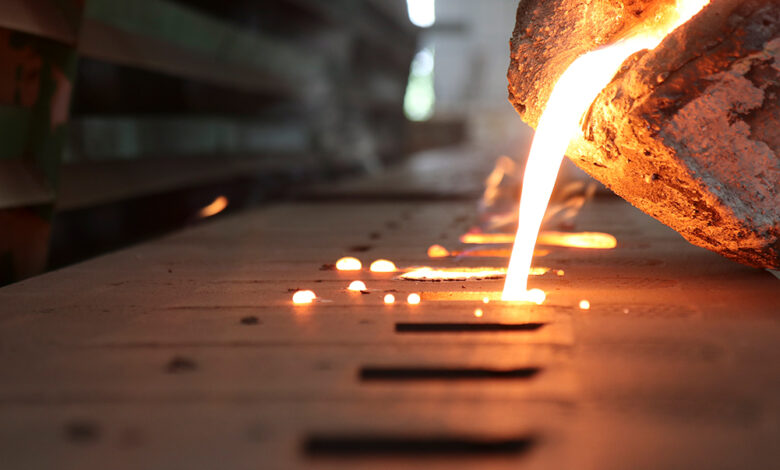
Millions of products are created every day, and depending on the industry, different techniques can be used. One of the most popular processes to create new items is investment casting, and it is probably the oldest form of manufacturing. In this article, we are going to tell you more about this process, how it is made, what it is, what its purposes are, and where it is used. So, continue reading if you want to find out more about this technique and why it has been around for thousands of years.
What is it?
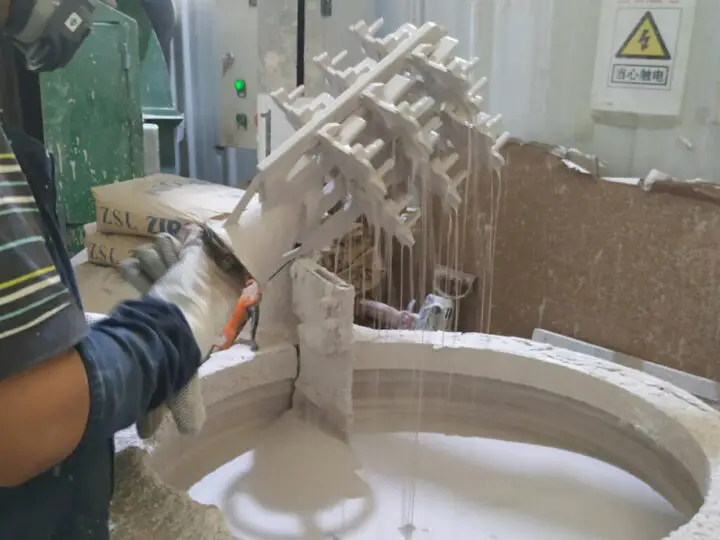
By definition, investment casting is the process where molds are used to create complex and detailed products and items. It is based on the long-wax casting process, and it is probably one of the most used processes in manufacturing.
This technique has been used for more than 5 thousand years, and even though some things have changed in the process, there are still steps that have remained the same. There are many different materials that can be used for this technique, and it is one of the most versatile ones. With it, you can create items made of brass, aluminum, stainless steel, and even glass.
Purposes
This process is most commonly used to create items and components that are complex and extremely detailed. The products that are made with this process are usually with tinner walls, they have a better surface finishing, and are much more durable when compared to the items that are made by sand casting.
Note that with this process, manufacturers can produce items that are of similar shape and size, and the mold that is made for the process can be used for the creation of different items. Because of this, this is one of the most popular processes when manufacturers need to create detailed and durable items that can be used in many different industries.
This is also the most commonly used rapid prototyping technique and it is the one that allows manufacturers to start the compiling process faster. The designers are able to create complex molds and designs, and the casting is finished faster, allowing manufacturers to create products in bulk without any delays.
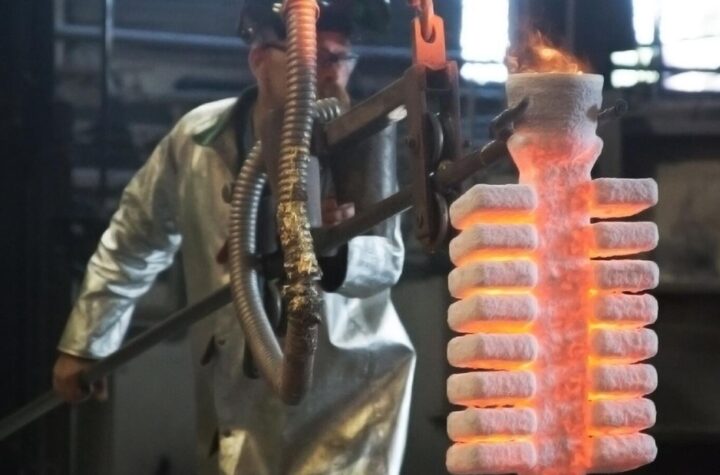
Casting process
Depending on the manufacturer, there can be between six and eight steps to finish this process. Now, we are going to talk about the most common steps, and note that some of them can be divided into several other steps, or they can be combined together to finish the whole creation faster. The exact number usually does not matter, as long as everything is done step by step, timely, and correctly.
The whole process starts with the creation of the wax patterns, and this is done when the manufacturers pour wax in the already made metal mold. Note that the mold needs to be previously made, and this is where the designers have all the creative freedom they need. When the wax pattern is created, then the wax tree needs to be assembled. This is used in industries where there are a lot of different small parts, and making them one by one requires a lot of time. When the wax tree is assembled and used, a lot of smaller parts can be manufactured at the same time.
Once that is done, a shell structure is built. The shell should be added around the tree, and later on, this shell will be used to add the molten metal that will be poured into it. Note that there are two main ways on how to build this shell and they include slurry coating and stucco coating. You can learn more about these ways to build the shell, and why waiting for it to be formed is an extremely important part of the process.
When the shell is fully built and formed, then the wax needs to be removed. The first process used to remove the wax is called steam-dewax autoclave and for this part, a machine removes it, and the wax can be later on reused for the same or a different purpose. The second option manufacturers have is to use a flashfire over, and this process leaves a clean shell without any leftover wax. The negative side is that the wax from the second process cannot be reused. Note that both methods are used, so ultimately one is not better than the other, and it is all a personal preference.
After the wax is removed, then the metal or the alloy needs to be poured into the shell. First, the metal is preheated until it becomes liquid and the shell needs to be preheated as well so that it does not cool off the alloy too quickly. When the metal is poured and cooled off, the shell needs to be removed. Manufacturers use different tools and processes to remove the shell, and it all depends on the type of metal, shell, and the preferences of the maker.
After that, the items from the tree are removed, cut, and finished to perfection. Note that when it comes to bigger objects, the wax tree is not used, and they can be individually cast as well.
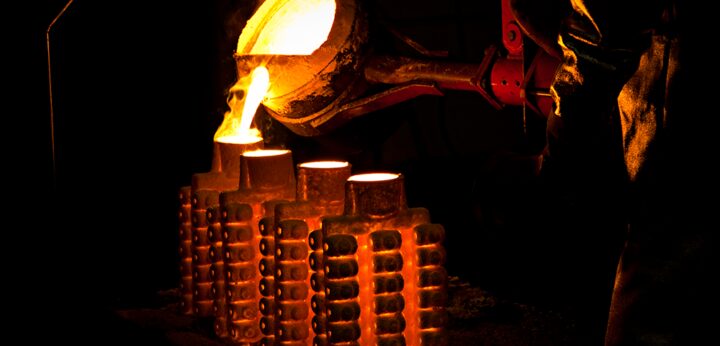
Conclusion
There are many reasons why people choose this technique when it comes to manufacturing, and some of the biggest advantages of this process include the ability to create extremely thin items, the fact that products with extremely complex details and designs can be produced, as well as the excellent surface finish. Note that there is almost no material waste, and if chemicals are not used in the shell removal process, this is an environmentally-friendly technique as well. With it, a wide variety of materials can be cast, and it does not require drafts for the mold design.
This technique has almost no disadvantages, and the only limit that has is that items cannot be with really large dimensions. There is a limit to the size and manufacturers need to pay attention to that if they want to be successful. This technique is relatively expensive, and the labor cost may be really high.
This technique allows manufacturers to produce a variety of different items and depending on the needs of the clients, unique items and products can be cast.