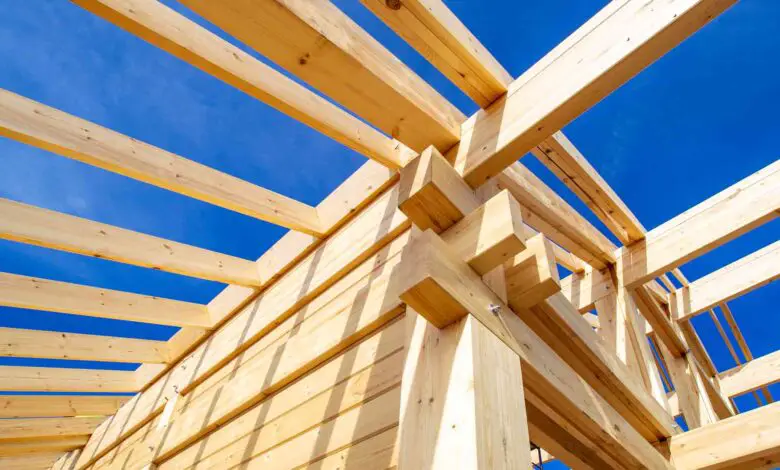
Lumber prices have soared over the past few years, leaving many wondering why an essential building material has become so costly. Several factors have combined to drive lumber to record high prices, impacting home builders, renovators, and consumers alike.
So you’re asking, why is lumber so expensive? Read on for some of the most relevant reasons.
Supply Chain Disruptions
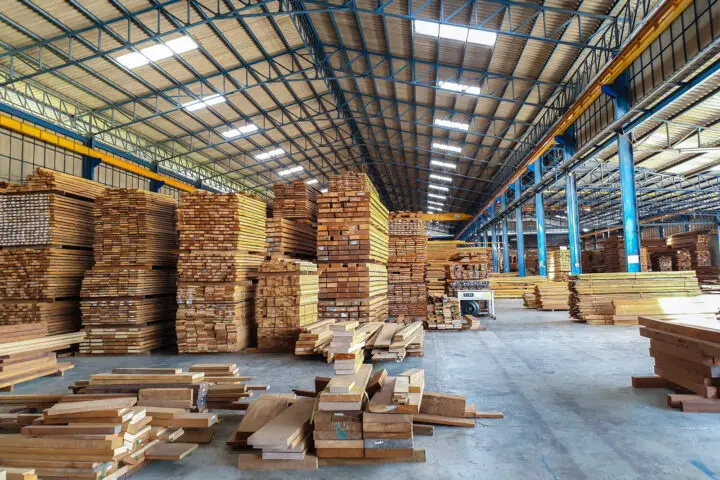
The pandemic caused significant supply chain disruptions across industries, severely impacting lumber production and transportation. Sawmills cut back on operating levels early in the pandemic due to reduced demand and labor shortages.
However, demand resurged faster than mills could restart production. Shipping logjams and trucker shortages further constrained supply. While mills are returning to pre-pandemic operating levels, it has taken time to catch up.
Surging Home Building and Remodeling
As people stayed home more, many decided to build new homes further away from urban centers or remodel existing ones to allow working from home. Millennials also entered the peak home-buying age, fueling demand for housing.
During the pandemic, the huge boom in home remodeling projects and improvement spending, combined with strong demand for larger suburban and rural houses, led to record lumber usage in residential construction.
More new-home construction is also being driven by underbuilding in prior years and positive demographics, with construction expected to continue strongly in 2024 as well, especially in southern and western states, seeing an influx of new residents. This magnified demand ripples across the entire lumber supply chain.
Tariffs
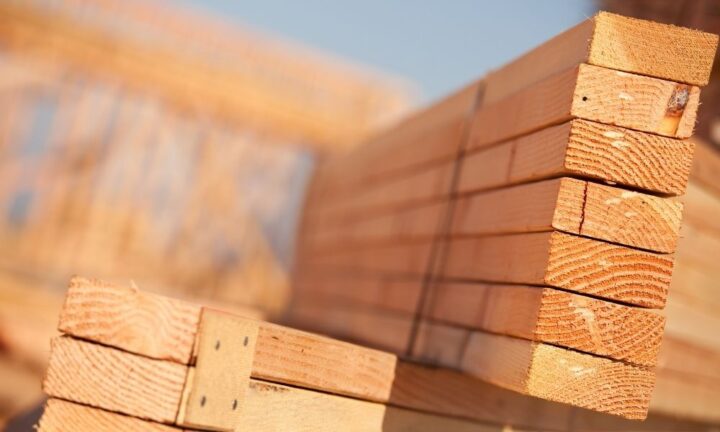
Trade policy has also impacted lumber prices. In late 2021, after a suspension agreement expired, the U.S. doubled tariffs on Canadian lumber to 18%. As Canada supplies over a quarter of America’s lumber, these tariffs have raised prices for U.S. consumers and builders while benefiting domestic lumber producers.
Weather Events
Weather Events Climate change has made natural disasters more extreme and frequent over the past decade. Devastating wildfires, powerful storms, flooding events, droughts, insect infestations, and other occurrences have severely damaged supplies of standing timber, log supplies, and production capacity in sawmills across forestry regions.
For example, pine beetle infestations enabled by warmer winter temperatures have destroyed vast stretches of Western forests in the US and Canada. The beatles have decimated over 90,000 square miles of pine forest since the 1990s. Storms and wildfires also limit access to forest lands for regenerative harvesting. According to the National Interagency Fire Center (NIFC), in 2023 alone, wildfires burned over 2.6 million acres of US forest lands.
The increasing frequency and destruction of climate events constrain supply and logistics across the entire forestry and lumber production chain. Even after temporary weather impacts subside, replanting trees and returning damaged mills to capacity takes years, worsening long-term supply issues.
Strong Renovation Outlook
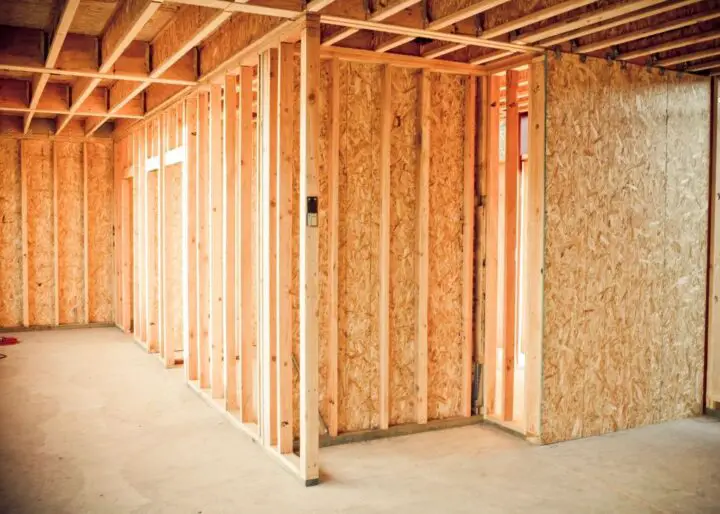
With high home price appreciation, more homeowners are tapping into their home equity to fund renovations. Others who are remodeling for resale can make back renovation costs quickly in hot markets. This demand ripples across the supply chain. Even after lumber prices retreat from 2022 highs, strong renovation demand should persist, limiting price declines.
When Will Prices Fall Back?
High prices have led sawmills to maximize production, and supply chain impediments should gradually ease. As supply rebounds, there is optimism that lumber could return to more normal pre-pandemic pricing levels in 2024. Much will depend on whether home building and remodeling remain red-hot or settle down. Any new supply chain shocks could also impact the pace of decline.
Navigating Ongoing Lumber Price Volatility
Extreme lumber price swings make budgeting and planning difficult for contractors, renovators, and builders. As the market remains unstable, stakeholders across the building industry must implement creative solutions to mitigate cost risks. Consider the following strategies:
Lock in Pricing
Forward contracts allow buyers to lock in lumber packages at a fixed price for future delivery, usually for a small premium. This insulates against further spikes, although you may sacrifice gains if prices drop quickly.
Contractors can hedge against 100% of expected lumber needs or a portion, balancing price stability with flexibility to benefit from market changes. Lumber wholesalers and wood product distributors usually offer forward contracting or fixed pricing programs.
Smart renovation budgeting tools can even integrate future pricing data into estimates and plans for projects spanning several months.
Use Price Contingencies
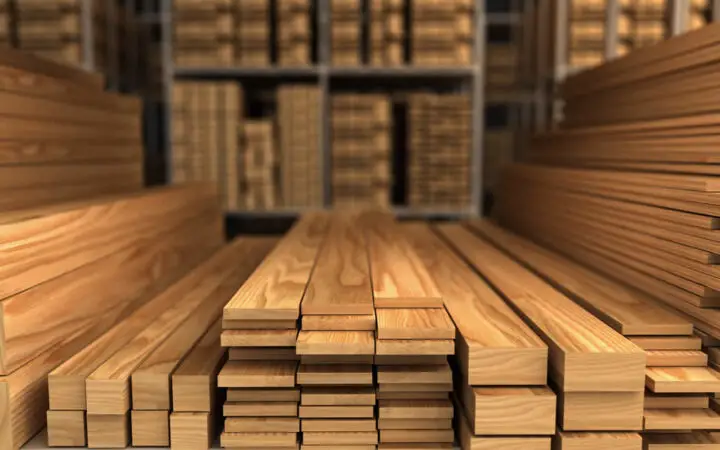
For renovators or builders signing fixed-price job contracts during volatility, add contingencies allowing you to increase prices if lumber rises past a threshold before job completion. Including benchmark price indexes and transparent cost, pass-through terms can help balance price protection for both contractor and client.
Substitute Materials
Consider using different construction materials that do not face the same supply issues, like steel beams and columns, instead of wood framing. Recycled plastic or composite lumber for outdoor decks and landscaping can also help sidestep volatility. If flexibility allows, shift to materials unaffected by lumber markets.
Get Creative with Design
Architects are increasingly designing homes with different wood layouts, sizes, and structural load distributions that allow for eliminating non-essential lumber. Simple design tweaks like removing embryo ceilings or using higher-grade plywood can make a difference. Consider consulting an architect familiar with designing for efficient lumber usage.
Use Software Tools
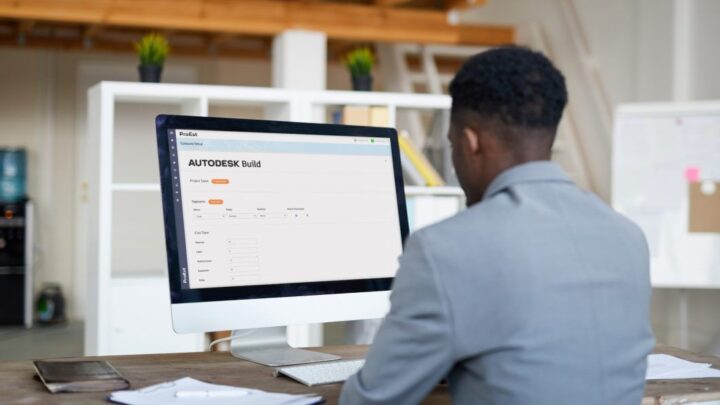
Software platforms like ProEst and StatCost analyze substitute materials and design changes to optimize lumber usage on construction projects. Input your builds to identify savings options. ProEst even uses historical pricing data to estimate optimal cost timing for purchasing lumber.
Add Schedule Buffer
Build additional time cushion into renovation or construction schedules to account for potential delays in obtaining lumber and other volatile materials—plan for longer lead times for framing lumber, plywood, OSB, and other wood products.
Tracking markets, leveraging technology, and getting creative operationally can help builders and contractors smooth out profitability swings during recurrent price spikes. Staying flexible and proactively addressing lumber expenses will remain key for the industry.
Lumber prices have soared to dizzying heights over the past two years thanks to a perfect storm of factors hitting supply and intense demand. With mills ramping up capacity, there is hope lumber will reverse course into 2024. In the meantime, contractors, builders, and homeowners have options to navigate price volatility. Staying flexible and proactively addressing lumber expenses will remain critica