Types of Plastics Used in Injection Molding
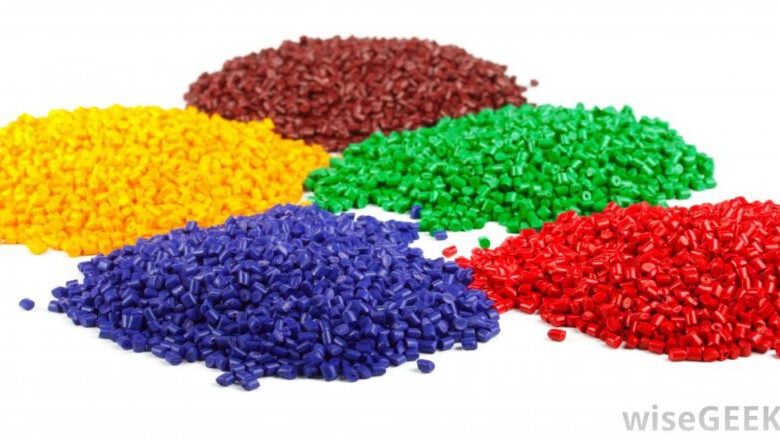
The discovery of plastic was revolutionary for mankind as it allowed us to manufacture all kinds of parts and items that we use on a daily bases.
We create these parts and items through injection molding, which is the process of putting molten materials such as plastic into a mold that can be used for mass production.
These molds come in all shapes and sizes depending on what the part or item is. The material used in plastic injection molding comes in the form of thermoplastics, and this material is can go through the phase of heating and cooling repeatedly depending on its use.
But what are the types of thermoplastic polymers used in this process? We will provide an answer to that question in this article so don’t go anywhere.
ABS – Acrylonitrile Butadiene Styrene
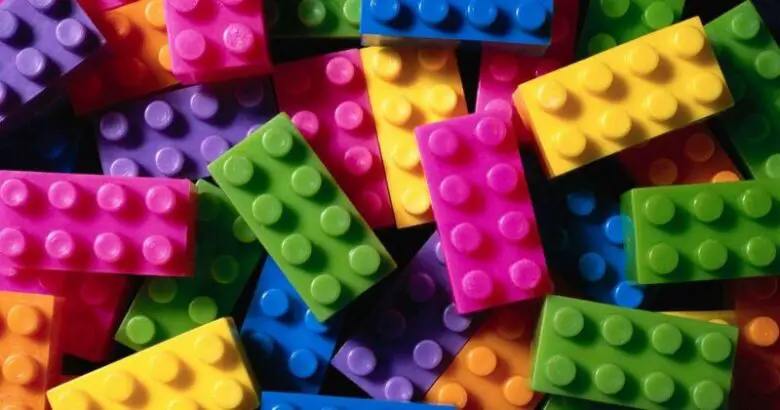
ABS is a type of material that consists of three monomers which are the ones in its name.
This thermoplastic is very versatile due to its components, which are responsible for its flexibility and lightweight. Because of this, ABS is used in molding and can be made in thousands of items that we use every single day.
One of the best features regarding ABS is that the material can easily be modified to better suit the needs of manufacturers. These modifications can impact the item’s resistance to various conditions such as heat, cold, toughness, etc.
Due to its ability to be easily modified, ABS can go through various processes without impacting the quality of the material. The final product shares the traits of the material and can go through different processes to add or improve those set traits.
For example, if you mold ABS on lower temperatures then the product will be very durable and prone to many types of physical damage. If ABS is molded on higher temperatures, then the product will have heat-resistant properties as well as gloss.
Some of the best uses for ABS include LEGO bricks, golf clubs, all kinds of kitchen appliances, as parts in the automotive industry, and tons of other.
Polyethylene
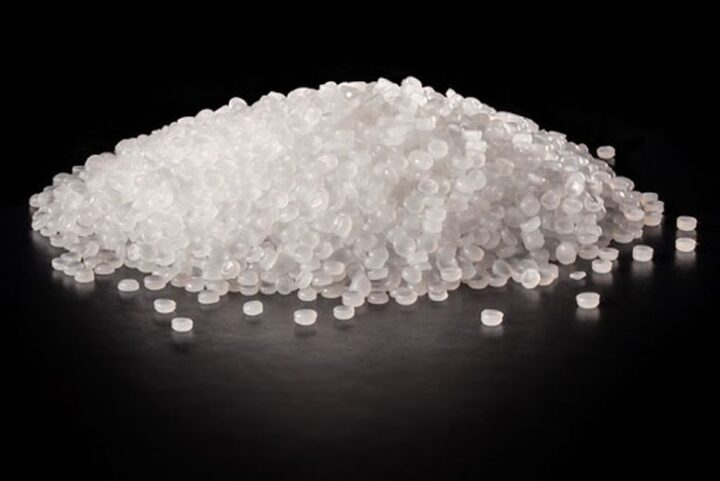
Polyethylene is significantly more versatile than ABS due to its crystalline structure that can be applied to hundreds if not thousands of industries and for millions of products.
This plastic was discovered in the 50s and has seen its use ever since. Polyethylene further separates into two materials used in injection molding; these are High-Density Polyethylene or HDPE and Low-Density Polyethylene or LDPE.
This material has numerous advantages over its rivals in the industry, and some often are its impact resistance, strength, moisture resistance, and quite possibly the most significant one, its ability to be reusable.
This material is very dense, and this is yet another big plus. The more dense Polyethylene is means better heat resistance, better strength, more rigidness, etc.
Some of the uses for Polyethylene include bottles, containers, plastic bags, etc.
Polycarbonate
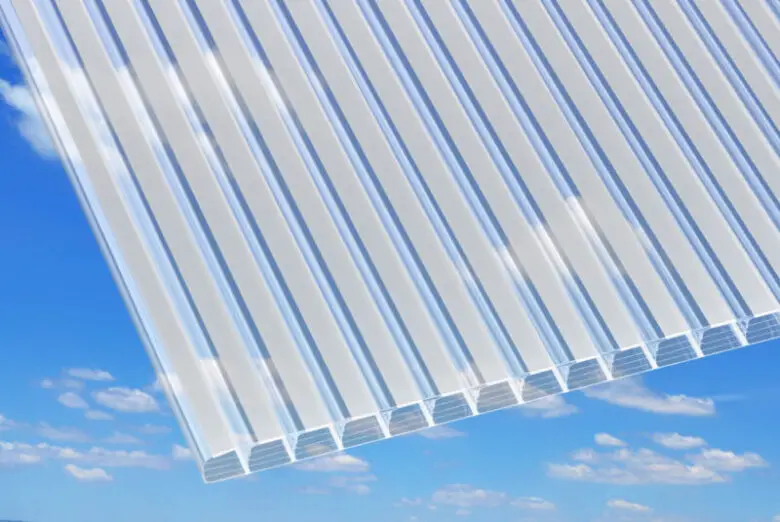
Polycarbonate is quite possibly the toughest plastic used in injection molding.
The differences in impact resistance and toughness between Polycarbonate and the rest of the materials used in this process are incomparable.
Because of this, PC plastic is mostly used for the production of bulletproof glass, bulletproof vests, medical devices, various parts for the automotive industry, DVD disks, lenses, and tons of others.
PC has the ability to undergo severe deformities without even cracking under the pressure applied.
If you’re interested in injection molding and finding plastic mold companies that will manufacture your goods, then consider visiting Moldall for more information regarding it.
Polyamide
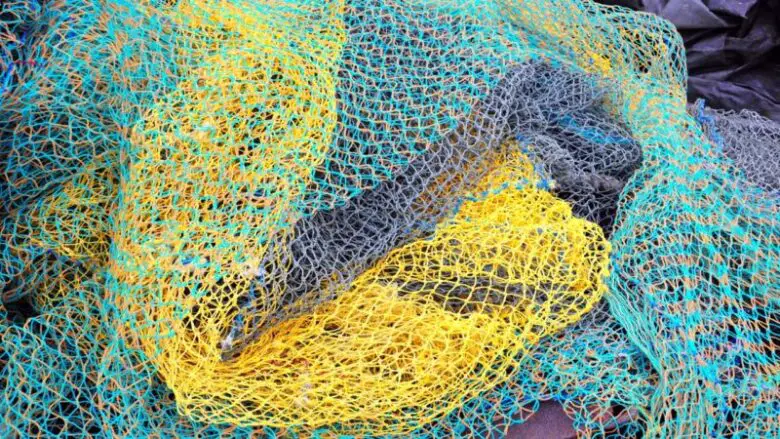
Polyamide is the formal world for Nylon and we all know how popular Nylon is. The material gets its popularity because of its electrical properties, amongst other things.
It is one of the few plastic materials that have this property, while others include chemical resistance, wear-resistance, and toughens. Nylon is super resistant to nearly all types of damage such as impact damage, chemical, and abrasion.
This material is very exciting and has huge potential for manufacturing parts in various industries such as the medical industry, the automotive industry, sports, apparel and footwear, and tons of others.
Every item that requires chemical resistance is mostly manufactured through Nylon.
High Impact Polystyrene
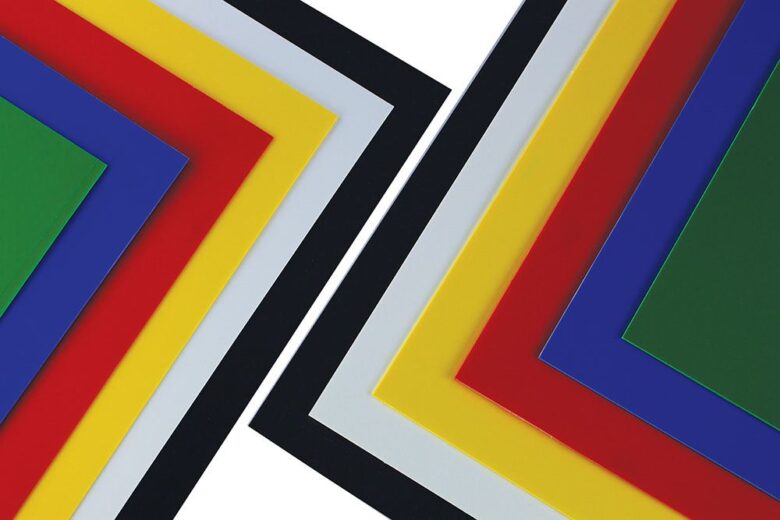
Polystyrene is the parent of High Impact Polystyrene and this material is yet another that is quite popular with the manufacturing industry and in the use of injection molding.
Polystyrene is rarely used on its own and is frequently combined with other materials to get the desired outcome. This is because Polystyrene is quite impact resistant but lacks in other areas. When combined with other materials, it gets the name High Impact Polystyrene or HIPS.
The most popular form of HIPS is when combining rubber and crystal styrene. The great thing about HIPS is that it is very cost-effective and very cheap to produce. It has good stability and even better rigidity.
Every HIPS comes in grades and the material is generally non-toxic, meaning it can be manufactured into containers that can store food.
One thing regarding HIPS is that it is highly flammable. The industry takes care of this by combining other flame-resistant materials with it.
Polypropylene
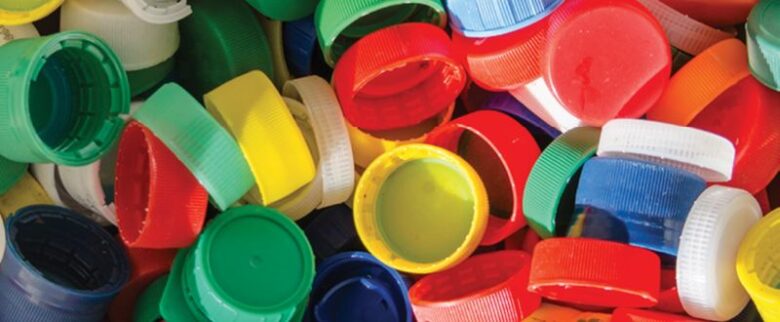
The last plastic used in injection molding that we’ll be talking about is Polypropylene.
Shortly known as PP, Polypropylene is highly flexible hence why it’s so popular. Flexibility with plastic is a very in-demand trait that puts PP among one of the most used plastics in injection molding.
PP is very resistant to stress and crack, can perform excellently underwater, acid, and various toxic detergents, and has a high melting point.
This puts it amongst some of the most popular types, and for good reasons.
With all that, the best use for PP is for manufacturing food containers, utensils, rugs, in the automotive industries for producing care batteries, and anything else that would require protection from chemicals, stress, etc.
These are some of the types of plastic used in the process of injection molding. Choosing the desired type should be done based on the needs of your product and not because of the costs for production.