Accurate Temperature Monitoring to Ensure Concrete Durability
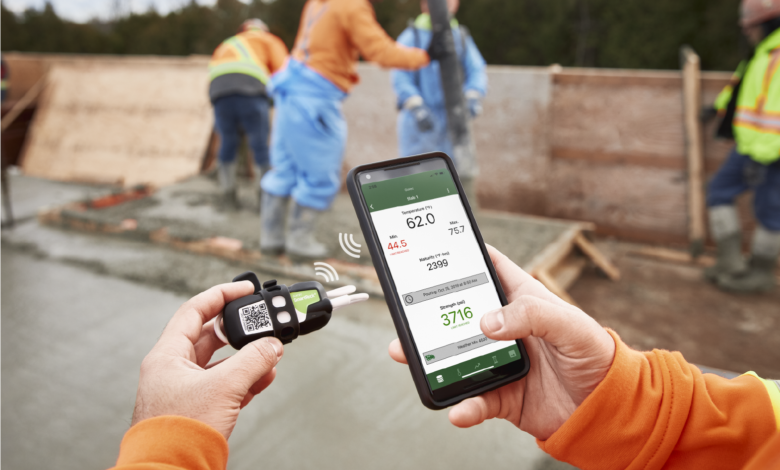
Contractors must monitor the temperature of concrete as it cures, as the concrete plays a key role in a structure’s integrity. Monitoring this temperature becomes more important in extreme weather conditions because the concrete is subject to changing environmental conditions during the mixing and curing phases. Freshly poured concrete, when exposed to temperatures outside the normal range, will be compromised in terms of its strength development. The same is true when the concrete does not preserve enough moisture.
Keeping a close eye on the temperature helps to avoid issues in the future. By monitoring these temperature variances in a concrete slab as it cures, the contractor can take steps to ensure the strength, quality, and durability of the concrete. The easiest way to monitor the temperature is with sensors designed specifically for this purpose, and these sensors can be found at doka.com.
Concrete Temperature
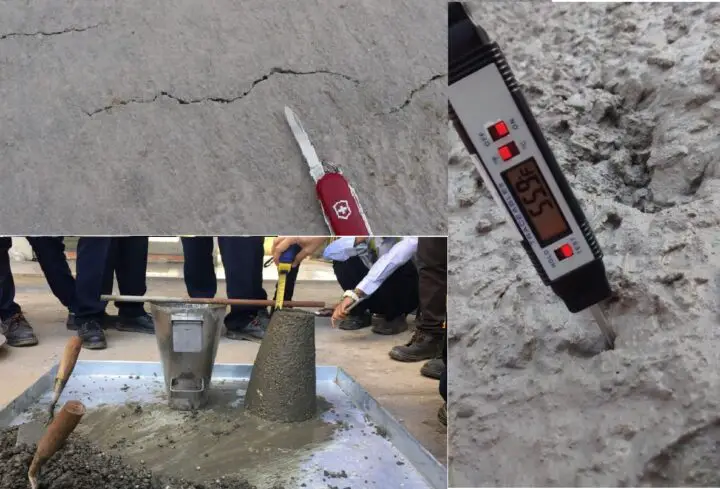
Monitoring the temperature of concrete is not a one-time job. The temperature generally peaks around 48 hours after it is poured. It then stays at that temperature for about a week. Larger structures generate more heat, and other factors play a role in the temperature. This includes the air temperature, the differential temperature, and the temperature of the concrete mix when it was poured. Continue monitoring the temperature until the concrete is fully cured to ensure it achieves full strength. Do not build on it until the strength is reached. The actual hardening of the cement may take three weeks or longer.
Problems That May Arise as the Concrete Cures
As the cement and water in the concrete mix, hydration occurs. This chemical reaction generates heat. The heat becomes trapped and cannot escape fast enough. As the core is heating, the exposed area cools. When there is a large difference between the core of the concrete and its surface, problems arise.
Thermal cracks may appear in the concrete, and these cracks increase the permeability of the concrete. Air and water can then make their way into the concrete. When they do, the structural integrity and durability of the concrete are negatively affected.
Some people might assume the hotter it is outdoors, the faster concrete will cure, and this is a good thing. However, the hydration reaction rate of concrete increases as the temperature increases. While the concrete does increase in strength at a more rapid rate, the final strength decreases. The hardened concrete’s physical form isn’t as structured due to the fast hydration reaction rate. Monitoring the temperature throughout the curing process leads to a strong and durable end product.
Extremely cold temperatures are also not good for concrete as it cures. Water can freeze in the concrete capillaries if the temperature drops to 28 degrees Fahrenheit. When the water freezes, it expands, and cracks may appear in the concrete. If the concrete freezes before it reaches 500 psi, its strength drops. This drop can be up to 50 percent of the strength of a fully-cured concrete structure.
Why It Is Important to Monitor the Concrete Temperature
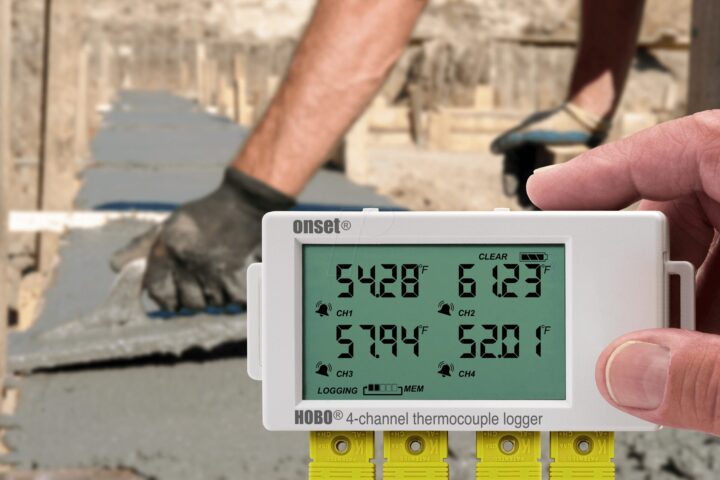
Concrete won’t solidify under the wrong conditions. The quality of the concrete structure will decline, and the safety of those near the structure decreases. When the contractor monitors the temperature, steps can be taken to prevent complications.
Furthermore, monitoring the temperature lets the contractor know when it is safe to build on this structure. The monitoring process eliminates unnecessary delays. Workers can safely continue with the project knowing the concrete has properly cured.
What Can Be Learned From Monitoring the Concrete
Monitoring the concrete will help the contractor know when temperature differentials exceeded safe limits. In addition, the monitoring process allows them to see if the concrete cooled adequately in the first 24 hours after being poured. They can evaluate the core temperature at different stages of the curing process and determine if temperature control strategies must be used. Monitoring the temperature will also give them peace of mind if they are able to prove the temperature remains consistent throughout the curing process.
Controlling the Concrete Temperature
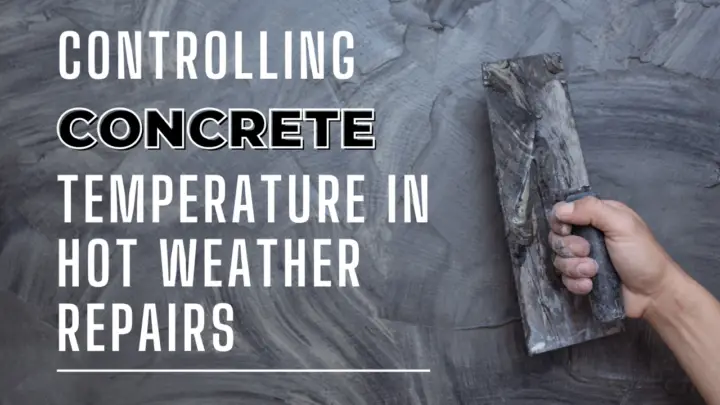
At times, temperature control strategies must be used to preserve the strength of the concrete. Several methods may be used to control the temperature of the concrete as it cures. Two methods are used during the dormant and strength-gain portions of the hydration process. The contractor may choose to optimize the mix design or they might control the curing properties that affect the concrete’s temperature. Some contractors choose to use a combination of these two methods.
Mix Design Temperature Control
Determine which type of concrete should be used, as the type determines the amount of heat generated. Finer cement, for example, generates more heat. The contractor should make this determination based on their knowledge and experience.
Supplementary materials can help keep the heat down during the hydration phase. For example, adding slag to the cement helps keep the heat down. In addition, admixtures can be used to control how long the dormant period lasts, but they rarely have an effect on heat generation.
Environmental Controls
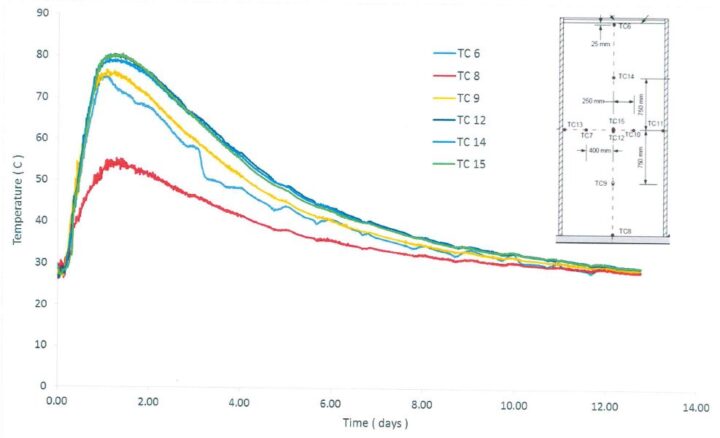
Environmental controls may also be used to ensure the concrete cures properly. Ice or liquid nitrogen may be added to the concrete water mix when it is hot outside. The ice or liquid nitrogen will help cool the concrete. Avoid pouring the concrete during the hottest part of the day, and keep an evaporative retarder on hand to use if the water evaporates rapidly.
When it is cold outside, steps may also be taken to control the curing of the concrete. Never pour concrete over frozen ground. Always use heaters to thaw the ground and remove any snow or ice before pouring the concrete.
Concrete sensors are of great help in monitoring heat generation, concrete strength, and more. Every person working with this material should use sensors so they can monitor the curing process from start to finish. The sensors ensure problems don’t arise and save the contractor money in the long run.
However, the choice of sensors is also of great importance. Ensure they are purchased from a reliable company, one with a track record for excellence. The monitoring process is only as good as the sensors used, so don’t skimp in this area. Invest in high-quality sensors for the best results every time.